How we freed up 10 hours of clinical time by re-organising our consulting rooms
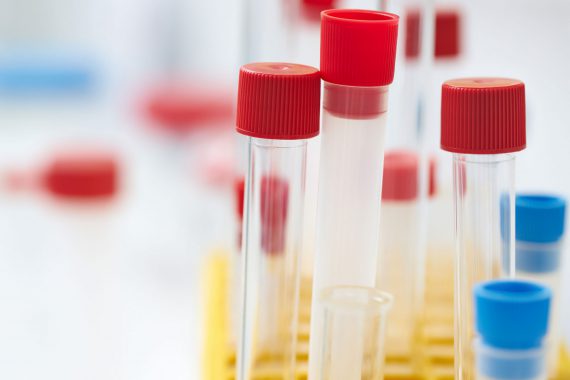
What we did
We are a five partner, 8,500 patient, urban practice in Sheffield. We decided to improve the surgery environment, so had an afternoon of training on the principles of the 5 Ss for all staff. 5S is an acronym of Japanese words describing a method of making processes and the environment safer. In English, they are:
Sort– We got rid of everything we didn’t need from the rooms, which turned up some things we couldn’t even remember what they were for.
Set– We made sure every item had their set place in the room, which was clearly labelled. We also organised the items by how often we used them – regularly used items were in easier reach than those we use more rarely.
Shine– We built in a daily cleaning routine. With the lack of clutter this was much easier.
Standardise– We made sure the places we put equipment were standardised across the surgery, for example all consulting rooms had specimen bags in the fifth draw down – easy for people moving rooms. This saves time, and also helps us restock easily – if a shelf is labelled for a certain item, but is empty, we know we need to order more of that item.
Sustain– We have continued practising and repeating these processes, linking it to the jobs we do.
Challenges
Committing to the time was a challenge. Building the training, carried out by a group from NHS Improving Quality (NHSIQ), into an afternoon where we would have our practice meeting anyway helped, but having the senior team of GPs and our practice manager on board was essential. We managed to organise most rooms within this one afternoon training session.
Allowing other people (both other staff and those running the training session) to look closely at our rooms was potentially very uncomfortable. Asking for volunteers to offer their rooms to start the process worked well by building confidence in the process and in our approach to it.
Some people were concerned that standardisation of rooms and spaces would mean that they would need to sacrifice their individual preferences. This was not found to be a problem. Once the basic equipment was installed in a standardised way, the addition of specialised or individual items could be done, as long as 5S principles were otherwise adhered too.
Results
It has saved time in the consultation because everyone knows where to look, staff no longer have to leave the room to track down missing stock and has made it easier for staff to work in different rooms from where they might work usually. A conservative estimate would be that it saves an average of five minutes per day per working clinician, which would be 10 hours a week of clinical time saved in our surgery.
The exercise was also fun and developed a sense of productive team working. One or two rooms did not get the 5S treatment on the day, and staff asked to have time to do this at a later date, which has happened.
We think that any practice could give this a try, unaided – just follow the 5S principles. Although it really helped us to have the process explained to us by specialists, the real limiting step is committing to releasing time in the practice to do this.
This intervention was uniformly appreciated by all staff in our practice, and we are still maintaining the changes, and reaping benefits, with minimal effort.
Dr Iolanthe Fowler is a GP in Sheffield
Pulse July survey
Take our July 2025 survey to potentially win £1.000 worth of tokens
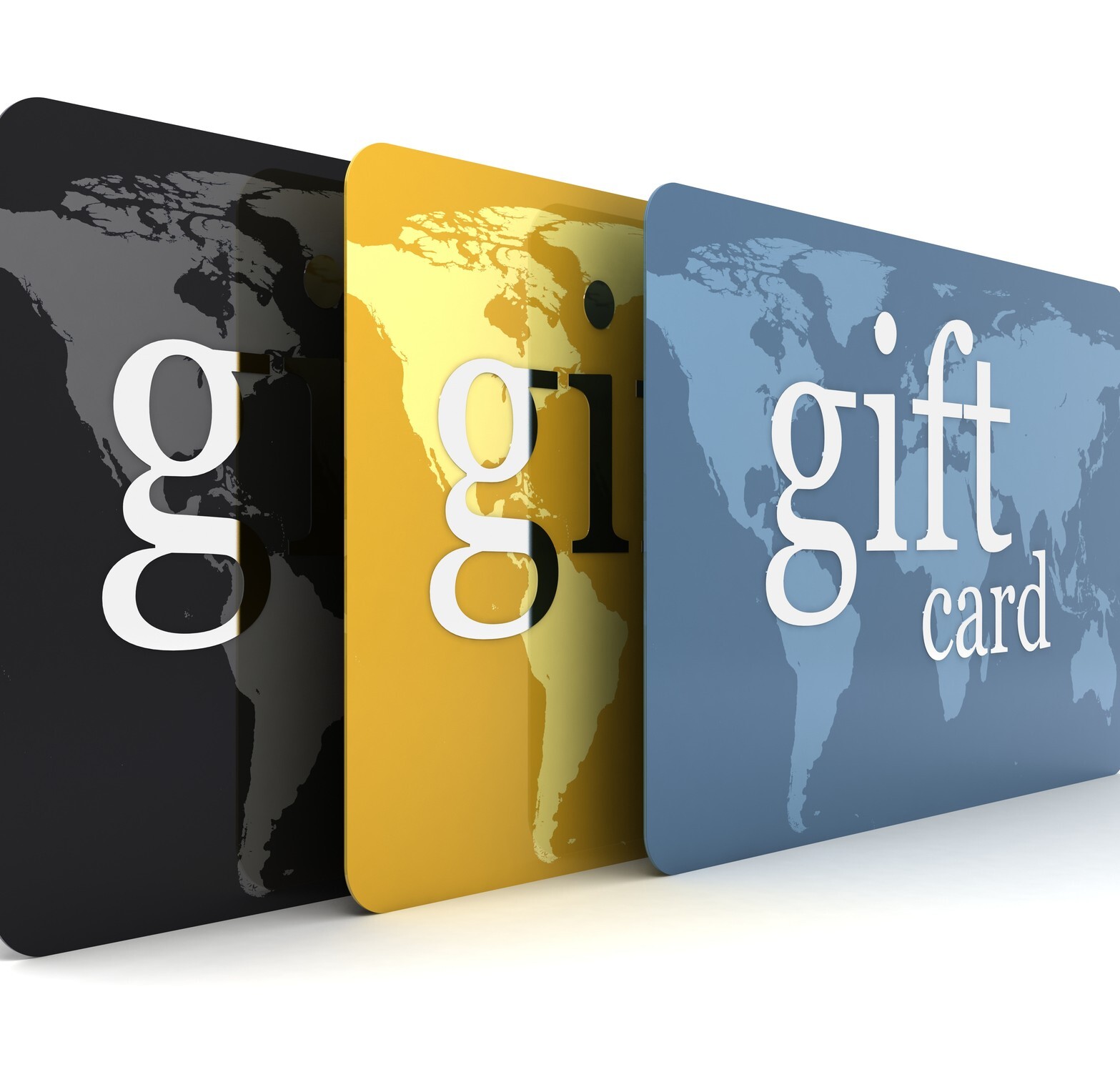